Sealing Cracks In Block Walls
Surface cracks, holes, or defects in poured concrete walls, honeycombed concrete, leaking form ties. Cracks in concrete block walls or missing mortar. Leaking deteriorated concrete blocks, blocks with large pinholes, hard-to-seal concrete blocks. Cracks in brick walls and mortar.
Concrete consists primarily of cement, sand, gravel and water. As the water in the slurry evaporates, the remaining ingredients cure into a hard, monolithic slab. Unfortunately, the curing process causes the concrete to shrink slightly, often resulting in hairline cracks. Larger stress cracks occur when a house settles or the ground beneath it shifts.
These types of cracks typically don't threaten the structural integrity of the house, but they do create an entry point for groundwater, insects and radon gas. Here, we'll show you a simple, effective way to patch cracks in poured- concrete walls. If you notice large, recurring cracks or bulging walls at your house, don't try to fix these conditions yourself.
The cracks might indicate a more serious structural problem; call in a structural engineer for an in-depth evaluation. Repairing the crack Several masonry patching products, such as hydraulic cement, do an adequate job of filling cracks in concrete walls. However, these products can fail after a few years if your foundation or retaining wall continues to move slightly, leaving you with little choice but to chip them out and start all over again. Spreadsheet tools engineers. We repaired a foundation wall, which had an 8-ft.-long crack that leaked water into the basement during periods of heavy rainfall. To permanently patch the crack we used an epoxy-injection system from Polygem, called the Liquid Concrete Repair Kit ($60).
Each kit contains a two-part epoxy crack sealer, two 10-oz. Tubes of Liquid Concrete Repair (LCR), a viscous epoxy that comes in a caulk-type cartridge, and seven plastic injection ports that deliver the LCR deep into the crack. There's enough material in each kit to repair a 1/16-in.-wide x 8-in.-deep x 8-ft.-long crack. Before you start, check to make sure the crack is dry. If the crack is slightly damp, dry it with a blow-dryer, then wait 15 minutes.
If it remains dry, proceed with the repair. However, if the dampness returns, water is still seeping into the crack and you'll have to wait for it to dry out on its own. First, scrub the crack clean of any loose concrete, paint or old filler using a wire brush (step 1). Remove all dust and debris with a shop vacuum. (10d) finishing nails partway into the crack, spaced 12 in. Apart (step 2).
You'll use them to align the injection ports with the crack. Open up the two containers of epoxy crack sealer and scoop out equal amounts of Part A and Part B; use two separate sticks to avoid contamination. Mix the two parts on a scrap board using a clean putty knife; blend until you achieve a uniform gray color (step 3). Spread some sealer onto the base of one of the plastic injection ports, being careful not to plug up its hole. Slide the port over one of the nails sticking out of the crack and press it to the wall (step 4). Install the remaining ports in a similar manner. Next, mix up a slightly larger batch of epoxy sealer and apply it to the entire crack using a 1 1/2-in.-wide putty knife or margin trowel (step 5).
Spread the sealer about 1/8 in. Thick and 1 in. On either side of the crack. Also, cover the entire flange of each injection port with crack sealer, leaving only the extended neck portion showing. Smooth out the sealer and feather its edges with a paintbrush dipped in mineral spirits. If the other side of the wall is accessible, see if the crack goes clean through. If it does, seal it up with crack sealer, too.
Allow the sealer to cure for 6 to 10 hours before injecting the epoxy. Thoroughly mix the LCR epoxy using the plunger rod that comes with the kit.
Place the LCR cartridge into a caulk gun. Starting at the lowest injection port, dispense the epoxy into the crack (step 6).
Continue squeezing the trigger until epoxy begins to ooze out of the port directly above. Remove the gun and plug up the port you just filled (step 7). Now insert the cartridge tip into the port that's oozing and squeeze the trigger to dispense the epoxy. Repeat this procedure for the remaining ports; plug up each one before moving on to the next. Allow the LCR to cure for five days, then cut off the necks of the ports with a hacksaw (step 8). If desired, you can patch the severed ports with a little crack sealer.
InspectAPedia tolerates no conflicts of interest. We have no relationship with advertisers, products, or services discussed at this website. How to seal cracks in concrete floors, foundations, walls, or other masonry: this article how to seal and repair of cracks in poured concrete slabs, floors, or walls. We list all of the current methods used to seal control joints or cracks that occur in those building surfaces, giving the properties, general procedure, and pros and cons of each method: control joint inserts, masonry caulks, radon crack sealants, semi rigid epoxy resin crack fillers, special poly urea caulks designed as a joint filler - polyurethane foam injection to seal cracks, grouts including portland cement, latex-modified, epoxy, modified epoxy-supported, and furan grouts or other products used to fill or seal cracks in concrete or other masonry surfaces & structures.
How to seal control joint & expansion joint cracks in concrete slabs Here we discuss how to choose among and apply the alternative methods for repairing or sealing cracks in masonry surfaces such as poured concrete floor slabs, concrete foundation walls, or brick or masonry block foundation walls. We describe use of epoxy sealants, polyurethane foam sealants, and hydraulic cement crack repair sealants. This article series describes how to recognize and diagnose various types of foundation failure or damage, such as foundation cracks, masonry foundation crack patterns, and moving, leaning, bulging, or bowing building foundation walls. Types of foundation cracks, crack patterns, differences in the meaning of cracks in different foundation materials, site conditions, building history, and other evidence of building movement and damage are described to assist in recognizing foundation defects and to help the inspector separate cosmetic or low-risk conditions from those likely to be important and potentially costly to repair.
Here we discuss: a list of materials used to fill poured concrete slab control joints. How to seal a cracked masonry foundation wall or floor slab.Typical concrete crack preparation for sealant with an epoxy product. Use of Polyurea as a control joint filler or crack sealant in concrete slabs (Polyurethane Foam Injection Method). Use of Epoxy-supported Grouts as a control joint or crack filler in concrete slabs or walls. List of the Types of Tile Grouts, their Bonding Agents and other Properties. Concrete expansion joint sealant products, epoxies, caulks. Use of Hydraulic Cement for Repairs in Concrete Slabs, Foundations, or Masonry Block/Brick Walls.
When should we not seal a foundation wall or floor slab crack? Warning: some crack sealing operations may make crack diagnosis or monitoring more difficult Watch out: First of all do not just seal a crack if the crack size, shape, pattern, location, or other evidence indicate that something important is going on with the foundation.
Further evaluation and choice of proper repair method may be in order. If for example we think that there may be active foundation movement or settlement going on and if that condition is going to be monitored for evidence of further movement, just pushing a flexible sealant or caulk into a crack is leaves some worries unattended: This photograph of foundation cracks attributed to concrete that included iron sulfide (pyrrhotite), provided courtesy of CCACB - Connecticut Coalition Against Crumbling Basements. The pattern looks like shrinkage but the crack width is larger than normal shrinkage cracking. Concete Crack Sealant hides ongoing movement: Using a flexible sealant in a structural crack may make it difficult to see small amounts of future movement since the sealant may stretch and tolerate small increases in crack width. This can increase the difficulty of crack monitoring and diagnosis. Sealant doesn't fix a structural problem: Using a sealant in a foundation or floor slab crack may fail to address the underlying cause of the problem such as foundation settlement or frost heaving which need to be addressed.
But some epoxy sealants are in fact also a repair: Some structural epoxies may seal and also 'repair' the damage in a structural sense. For example Sika produces epoxy resin & structural engineering systems for concrete crack repair using a structural injection system. We may decide to seal a cracked wall or floor slab anyway, to try to reduce water entry in a building, but remember the implications of sealing we've just listed.
Types of Sealant Repairs in Concrete & Concrete Structures Control joint sealant: control joints, designed to control where cracks appear in concrete placed horizontally or vertically, are themselves are sealed against water, frost, debris and to handle recurrent movement (listed below) using a flexible sealant. Recurrent movement: Seal and repair cracks in concrete using injection of either epoxy resin or polyurethane where recurrent movement is expected (in my opinion a flexible sealant is what's called for here) when the movement is considered normal, perhaps caused by traffic vibration or temperature swings, and where the movement is not threatening structural damage. Stop a water leak: Seal and repair cracks in concrete when it is important to quickly stop water leaking through a crack,seal those cracks in concrete using injection of either epoxy resin or polyurethane sealant. Structural repair: Seal and repair structural cracks: for some situations (usually where an engineer, expert in masonry repair has made an assessment), actual structural repairs are made using injectable epoxy resin and possibly in some (probably low-load) cases by using injectable polyurethane sealant. In my opinion (I'm not a P.E.) this application of injected epoxy resin is probably most-appropriate when cracks have appeared due to non-recurrent stresses. When we epoxy cracked structural concrete or a concrete slab that was broken by an initial installation error or by a subsequent event, we expect the repaired area to be as strong or stronger than if no crack were present.
Structural reinforcement: some sealant manufacturers such as Sika provide seal or wrap-and-seal systems that actually provide additional strength to existing concrete structures such as concrete columns. Structural reinforcing wrap systems may include use of synethetic fabrics, carbon fibre fabrics, and other wraps. These products might also be used on steel or concrete that has been damaged by weather, frost, corrosion. Surface repair: for working surfaces such as industrial work floors or parking decks cracked by spider-webbed shrinkage cracks that are non-structural, special 'healer-sealer' crack sealants may be applied.
Specialty Epoxy Resin and Structural Engineering Systems for Concrete The situations listed above are those of most-interest to owners of residential and smaller commercial buildings. Below are examples of additional applications of epoxy resins and sealants in construction: Anchoring epoxy products: used to inject into holes into which connectors such as bolts or post anchors will be placed. Bonding agent epoxies: used to promote secure bonding between abutting, often different materials. A special example is the use of segmental bridge adhesives that bond post-tension pre-cast concrete bridge segments to other structural members or to one another.
Epoxy resin adhesives are formulated for bonding concrete to concrete, concrete to other masonry, concrete to steel, and concrete to wood or to other substances. Overlay expoxy resin coatings: used as a coating on concrete surfaces for skid protection or for patching damaged surface areas. Some of these epoxy resin products are formulated for use as a high-friction surface or for use to repair spalled or chipped concrete surfaces. Special acknowledgement: some of this discussion was informed by reviewing products and engineering literature provided by. Sika Corporation, 201 Polito Avenue, Lyndhurst, NJ 07071 USA, Tel: 1-800-933-SIKA Website: Sika produces a wide range of adhesive, bonding, reinforcing and sealing products including automotive adhesives, building envelope adhesives, concrete admixtures, flooring and floor covering adhesives, repair & protection products, rofoing products, sealants, adhesives, waterproofing agents.
How to seal a cracked masonry foundation wall or floor slab To seal a shrinkage crack or a control joint crack in a poured concrete slab, regardless of whether or not it has occurred at an expansion or control joint, it may be appropriate to seal the surface to resist water entry and radon gas entry. Control joints are also sealed to provide a smooth and clean concrete surface which does not collect surface moisture or debris. Keeping surface water from entering at a control joint might in some cases also help avoid uneven soil settlement below the slab and tipped or heaved slab sections. To seal a control joint or expansion joint crack in a concrete slab use a flexible sealant designed for foundation crack repair or sealing. The radon mitigation industry offers special foundation caulks and sealants for that purpose as well. (If water is coming up through a concrete floor or slab, sealing cracks is probably not going to be enough - you need to address the cause of water below the floor.) List of Types of Materials Used to Fill or Seal Poured Concrete Slab Control Joints. Pre-fabricated control joint strips of plastic or other material.
Masonry caulks or flexible (typically polyurethane based) radon sealant caulks. Pproduct sources are listed at SEAL CRACKS BY POLYURETHANE FOAM INJECTION - live link just below. Semi rigid epoxy resin crack fillers (discussed in this article). Epoxy products intended for concrete expansion joints. These products are described and their sources listed below in our discussion of this method that includes injection ports and (usually) two-part epoxy resins injected into the crack.
Special poly urea caulks designed as a joint filler - polyurethane foam injection to seal cracks. This method is discussed below.
Separately we discuss this method in detail along with product sources at. Hydraulic cements for concrete or other masonry floor, foundation, or wall repairs of cracks & leaks Any sealant that is going to be used to fill a control joint in a slab needs to have the ability to bond to the sides of the cut or opening of the joint, to remain flexible over temperature and moisture changes, and to withstand both compression and expansion as the concrete moves in response to curing and in response to temperature and moisture changes. Epoxy, for example, is not generally used to fill the expansion joint in newly-poured concrete because the concrete is just too wet and has too much movement for the epoxy to bond and perform acceptably. Similarly, a special product would be needed to fill a control joint in concrete in very cold weather. Watch out: select the right product for your application.
Some crack fillers like the spray injection product Good-Bye Cracks elastic crack 'cover' product shown in our photo are not suitable for concrete. The manufacturer says this product can be used to fill cracks in plaster, drywall, and wood and that it dries to a flexible, paintable finish. Typical concrete crack preparation for sealant with an epoxy product ' sketch shows three common methods used to seal cracks in masonry walls in an effort to stop foundation leaks.
Click to enlarge any image. Cleaning a concrete crack for patching and sealing: The crack or expansion joint must be cleaned of all debris; power washing and vacuuming may work but inspect the crack or joint to be sure it is clean along its entire length. Otherwise the sealant may fail to adhere and the crack will leak. Wire-brushing or chipping the crack sides is not normally required when using an epoxy sealant.
(Traditional concrete or masonry patching (and plaster repairs), on the other hand, was traditionally applied after cracks were chipped and widened into an inverted 'vee' shape to help keep the patch material in the crack.). Mix the epoxy sealant according to the manufacturer's directions. Some low volume epoxy sealants are supplied in a dispenser which mixes the two parts together in the proper ratio automatically during dispensing from a tube (see your dentist for an example.) Other crack sealants such as prepared caulks, may come pre-mixed in a tube. Install the backer rod specified by the sealer manufacturer if you are sealing an expansion joint. The backer rod provides a flexible filler that keeps the sealant in the joint during curing and also reduces the total volume of concrete crack sealer epoxy needed. We recommend using backer rods also if sealing wide cracks in concrete walls or floors, but first you need to have those cracks evaluated to determine the cause as other important structural repairs could be needed first. Sand (clean, dry) may be used as a filler for cracks - an easier approach if you are repairing an irregular crack in a floor.
Sand should stop about 3/4' from the top of the floor surface to give adequate volume of sealer epoxy in the crack. Epoxy crack patch cure time: Keep traffic off of the sealed crack until the sealant has cured.

Typically a thin film will form on a crack filler epoxy in 8 hours, the sealant will be hard enough to withstand traffic in 24 hours, and it will fully cure in about a week. These notes are based on epoxy product application information available from. Use of Polyurea as a control joint filler or crack sealant in concrete slabs (Polyurethane Foam Injection Method) Polyurea joint filler products for concrete control joints have received attention for filling concrete control joints and is increasingly used in that application since this material is resistant to moisture, has high adhesion properties when used with concrete, and will cure in very cold weather. Polyurea sealant products are also reported to be useful in sealing control joints in 'green' concrete which has not yet had its full 28 day period of initial curing. An advantage of polyurea or polyurethane used as a crack sealant is that the flexibility of the material will accommodate slight seasonal or temperature-related movement that might otherwise cause new cracks in an epoxy-repaired structure or reopening of repaired cracks in a mortar or concrete-repaired crack.
Also in our experience, because the injected polyurethane foam expands after it is injected into a crack, you may find it easier to fill the crack through the building floor slab or wall than when using alternative repair methods such as epoxy or masonry repair kits. ' sketch (left) illustrates foundation wall crack repair using epoxy or polyurethane injection. List of materials, product sources, how-to for polyurethane foam crack sealant. See our separate article for details of the procedure for using polyurethane foam to seal foundation cracks and for a list of sources & brands of polyurea or polyurethane foam sealants, caulks, and crack repair kits. Use of Epoxy-supported Grouts as a control joint or crack filler in concrete slabs or walls Epoxy grouts are available which can be mixed and troweled into a concrete crack or joint.
These products are less flexible than the control joint fillers described above. In our opinion, an epoxy grout filler may work fine to provide a well-bonded repair to a stable wall or floor crack in an area where there is no anticipated further movement such as from temperature or moisture variations. Watch out: while epoxy, a material stronger than concrete alone, is sometimes used for structural repairs, if your building masonry (concrete, brick, masonry block) is cracking due to ongoing movement, settlement, frost, or other active or recurrent problems, unless those conditions are fixed, sealing a crack with epoxy will not prevent new cracks from forming. But read the manufacturer's intended application before buying an epoxy reinforced grout for building crack repair. Do not use the product where it was not intended unless a call to the manufacturer provides you with good information that it's acceptable to do so. On the one hand we like using a rigid material to fix a supposedly stable crack in a residential building since the fact that the patch is inelastic means it will be easy to see if there is ongoing or new building movement.
On the other hand, a small amount of moment in a foundation wall or floor slab due to changes in temperature will leave a flexible crack filler un-damaged and sealed where a rigid material may fail. List & Sources of Epoxy Grout Products & Structural Injection Concrete Repair Products. Elasta Gel 6170 Epoxy® flexible epoxy and expansion joint sealant, two component, no VOC, flexible epoxy resin which is rated for use on parking decks and, according to the manufacturer, can also be used to repair concrete spalling on such surfaces. Emecole Structural Repair Epoxy products, 50 E. Montrose Dr., Romeoville IL 60446, USA Tel: 800-844-2713, Website: www.emecole.com. Emecole 121 Premium - Fast Curing Crack Repair Epoxy.
Emecole 101 Original Formula - Crack Repair Epoxy. Emecole 40 - Concrete Deck Repair Epoxy. Emecole cargon fiber reinforcement products: used by professional repair contractors where a building wall suffers large cracks or bowing.
Basement Cracks In Block Walls
(Also see.) Quoting: Emecole Epoxies are recommended for structural cracks. Unlike polyurethane foams, epoxies will not expand.
However, they cure to an incredibly hard solid, making them ideal for structural repairs. Our two-component epoxies are strong, durable and reliable. After curing, Emecole Epoxies create a more powerful bond than concrete, resulting in an extremely strong repair. Epoxy grouts (ANSI 118.3 1988) for tile applications (watch out for proper tile surface cleaning within the cure time; cleanup is done using water).
Laticrete™ epoxy grouts. Mar-Flex Epoxy Injection Concrete Crack Repair Kit, Tel: 800-498-1411, Website: www.mar-flex.com Quoting: Low-pressure injection and repair of approximately 8-10 lineal feet. Contains the following; (1 jar 8oz.) Mar-flex Crack Seal (1 jar 8oz.) Port Adhesive (2) Wooden Sticks (12) Surface Ports and Caps (2 Cartridges) Mar-flex Injection Polyurethane/Epoxy Resin 1:1 (2) 3/8':24 Mixing Nozzles (1) Injection Hose Assembly with plastic shut-off valve (2 pair) Latex Gloves (1) Plastic Trowel (1) Wire Brush (1) Drop Cloth (1) Complete Instructional DVD. The company also offers low-viscosity crack filler that can be injected into both dry and damp cracks and a 'Seal & Peel' crack repair kit. Polygem Epoxy pastes, resins, & grouts, POLYGEM, Inc. Box 609 West Chicago, IL 60186, Tel: 888-446-3987, Website: www.polygem.com. Polyject #1001 LV for hairline to 1/16” cracks.
Polyject #1001MV for 1/16” to 1/8” cracks. Polyject #1001 HV for 1/8” to 1/4#148; cracks. Polyject #1001 EHV for over 1/4#148; cracks Quoting: Polygem, Inc. Manufactures epoxies, vinyl-esters and silicones for various industries and markets such as: Construction, Waterproofing, Mining, Industrial, Electrical, Zoological, Golf and DIY. Polygem, Inc. Has been custom formulating epoxies in excess of twenty-five years and has created over 1,500 unique formulations.
Ramset™ Epoxy Grout - a pourable epoxy resin, also can be mixed with sand and applied with trowel. Shor D 65-80®. Sika Corporation, 201 Polito Avenue, Lyndhurst, NJ 07071 USA, Tel: 1-800-933-SIKA Website: Sika produces a wide range of adhesive, bonding, reinforcing and sealing products including automotive adhesives, building envelope adhesives, concrete admixtures, flooring and floor covering adhesives, repair & protection products, rofoing products, sealants, adhesives, waterproofing agents. Other semi-rigid, epoxy products - contact us to add products & information - no fees involved Use of Peel-and Stick Surface Sealant Kits for Epoxy-Repair Cracks in Concrete Walls For building surfaces that will remain exposed and where cosmetic appearance is a concern, RadonSeal (and perhaps others) offers a stick-on injection port system that allows the crack material to be injected into a wall or floor crack to leave a smooth surface even with the existing wall or floor surfaces on either side of the crack.
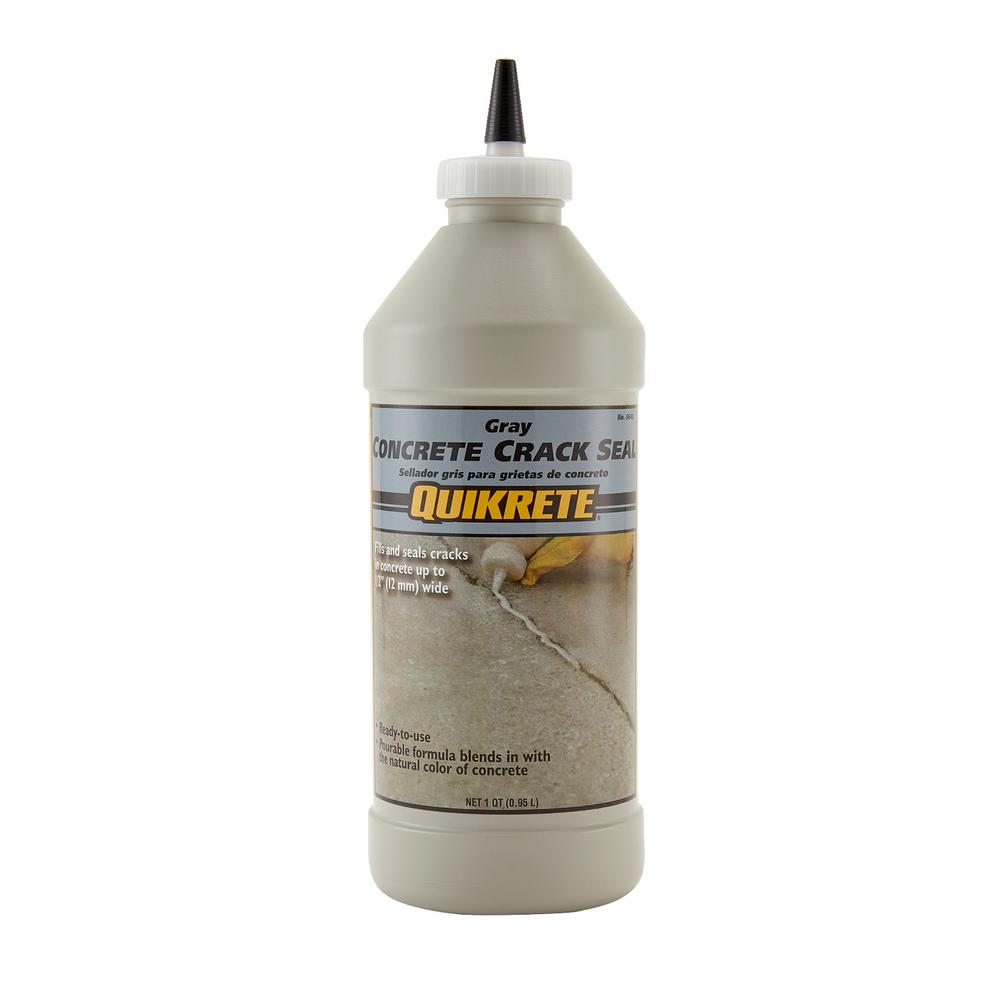
RadonSeal's Easy-Peel Sealer kit uses a surface seal that includes injection ports. After the injected sealant has cured, the surface seal and injection ports are peeled away from the repaired surface.
Quoting: RadonSeal Crack Seal and Port Adhesive 1:1 is a high modulus epoxy gel designed for surface sealing of cracks prior to injection and for attaching surface ports. It can also be used for bonding miscellaneous materials to concrete.As with any epoxy adhesive, surface preparation is critical. Concrete surfaces should be cleaned by wire brushing or other mechanical means. All loose or unsound material must be removed. Surfaces should be dry and dust free to insure a superior bond.
Application onto wet surfaces is not recommended. RadonSeal Crack Seal & Port Adhesive, Novion, Inc., 18 L'Hermitage Dr., Shelton CT 06484, Tel: 800-472-0603, Website: www.radonseal.com.
Mar-Flex Epoxy Injection Concrete Crack Repair Kit, Tel: 800-498-1411, Website: www.mar-flex.com The company offers low-viscosity creack filler that can be injected into both dry and damp cracks and a 'Seal & Peel' crack repair kit. How to Choose Between Using an Epoxy Crack Sealant & a Polyurethane Crack Sealant High Pressure or Low Pressure Slab or Foundation Wall Crack Sealant Injection Most foundation wall and floor slab cracks can be successfully filled and sealed using low-pressure injection such as that afforded by a caulking gun and cartridge of sealant, or similar device for both epoxy and polyurethane foam sealants. Professional polyurethane foam injection crack sealing applicators may use a high-pressure injection system using equipment that includes a pump or a device similar to an automotive grease gun and pressures up to 250 psi. Drilling to prepare injection ports along the crack may be required. Reasons to use an epoxy-based crack repair or sealant method.
Structural repairs are needed. Epoxy, properly mixed and installed, is stronger than the concrete to which it is bonding. But as we warn above, unless you correct the cause of ongoing (such as settlement or earth loading) or cyclical (such as water or frost) structural movement & cracking, new cracks will develop in the structure. Very fine cracks need to be sealed - so fine that it may be difficult to inject a polyurethane foam, but still possible to inject a low-viscosity epoxy sealant. For wider cracks use a higher viscosity epoxy preparation or consider a polyurethane injection approach.
Books & Articles on Building & Environmental Inspection, Testing, Diagnosis, & Repair. you are currently on this web page. 'Best Practices for Concrete Sidewalk Construction,' Balvant rajani, Canadian National Research Council. 'Design Considerations for Perlite Roof Slabs,' a chapter in 'Perlite Concrete Grade for Lightweight Concrete Construction', United Perlite Corporation., National Association of Home Builders Remodelers Council, NAHB Research Foundation, 1987. Ahmed, # Home Builder Pr (February 1991), ISBN-10:, ISBN-13: 9597., Rowlett TX, product literature, includes application instructions for this flexible epoxy resin concrete expansion joint sealer. 10/06/08.
Ramset™, Australia,. ™ Epoxy grouts., W.H. Ransom, E.& F. Spon, New York, 1987 ISBN 0-419-14270-3., Samuel Y.
Harris, P.E., AIA, Esq., ISBN 0-471-33172-4, John Wiley & Sons, 2001 General building science-DF ISBN-10: ISBN-13: 9728., David Watt, Wiley-Blackwell; 2 edition (March 7, 2008) ISBN-10: ISBN-13: 9039., M. Hatzinikolas, Y. Korany, Canadian Masonry (2005), ISBN-10:, ISBN-13: 9105., Robert G.
Drysdale, Ahmid A. Hamid, Lawrie R. Baker, The Masonry Society; 2nd edition (1999), ISBN-10:, ISBN-13: 9011., N.U. Ahmed, # Home Builder Pr (February 1991), ISBN-10:, ISBN-13: 9597., U.S.
Department of Energy Books & Articles on Building & Environmental Inspection, Testing, Diagnosis, & Repair. Our recommended books about building & mechanical systems design, inspection, problem diagnosis, and repair, and about indoor environment and IAQ testing, diagnosis, and cleanup are at the. Also see our.,. John Wiley & Sons, 2006.
ISBN-10:, ISBN-13: 9369, Hardcover: 320 pages, available from and also. See our of this publication.
for structural crack monitoring., U.S. Department of Energy., U.S. Department of Energy., Edgar O.
Seaquist, McGraw Hill, 1980 ISBN 0-07-056013-7 (obsolete, incomplete, missing most diagnosis steps, but very good reading; out of print but used copies are available at, and reprints are available from some inspection tool suppliers). Ed Seaquist was among the first speakers invited to a series of educational conferences organized by D Friedman for ASHI, the American Society of Home Inspectors, where the topic of inspecting the in-service condition of building structures was first addressed.
Williams, Kindle book, Amazon.com., Barry Richardson, Spon Press; 2d Ed (2001), ISBN-10: 041925210X, ISBN-13: 9108. Quoting: A professional reference designed to assist surveyors, engineers, architects and contractors in diagnosing existing problems and avoiding them in new buildings. Fully revised and updated, this edition, in new clearer format, covers developments in building defects, and problems such as sick building syndrome. Well liked for its mixture of theory and practice the new edition will complement Hinks and Cook's student textbook on defects at the practitioner level., Jack Bower, Butterworth Architecture, London, 1988, ISBN 0-408-50000 X. 'Avoiding Foundation Failures,' Robert Marshall, Journal of Light Construction, July, 1996 ( Highly recommend this article-DF). 'A Foundation for Unstable Soils,' Harris Hyman, P.E., Journal of Light Construction, May 1995.
'Backfilling Basics,' Buck Bartley, Journal of Light Construction, October 1994. 'Inspecting Block Foundations,' Donald V. Cohen, P.E., ASHI Reporter, December 1998. This article in turn cites the Fine Homebuilding article noted below. 'When Block Foundations go Bad,' Fine Homebuilding, June/July 1998., Stephen Showalter (director, actor), DVD,. J.
Gainville, Cantext publications (1983), ASIN: B0007C37PG., Hans J. Schultz, National Concrete Producers Association and the Canadian Masonry Contractors Association (1976), ASIN: B0007C2LQM., U.S. Department of Energy., U.S.
Department of Energy., National Association of Home Builders Remodelers Council, NAHB Research Foundation, 1987. 'A Hole in the Ground Erupts, to Estonia's Delight', New York Times, 9 December 2008 p. History of water usage in Estonia: (5.7 MB PDF) jaagupi.parnu.ee/freshwater/doc/thehistoryofwaterusagesystemsinestonia.pdf. 'Quebec Family Dies as Home Vanishes Into Crater, in Reminder of Hidden Menace', Ian Austen, New York Times, 13 May 2010 p. See.
'Quick Clay', Wikipedia search 5/13/2010 -. Florida DEP - Department of Environmental Protection, & Florida Geological survey (on Florida sinkholes: Effects of Sinkholes on Water Conditions Hernando County, Florida, Brett Buff, GIS in Water Resources, 2008, Dr. Maidment, Photos - Tom Scott, Florida Geographic Survey - Web Search - and - also see Lane, Ed, 1986, Karst in Florida: Florida Geological Survey Special Publication 29, 100 p. Foundation Engineering Problems and Hazards in Karst Terranes, James P. Reger, Maryland Geological Survey, web search, original source:, 2300 St.
Paul Street, Baltimore, MD 21218. 'Frost Heaving Forces in Leda Clay', Penner, E., Division of Building Research, National Research Council of Canada, Canadian Geotechnical Journal, 1970-2, Vol 7, No 1, PP 8-16, National Research Council of Canada, Accession number 1970-023601, Quoting from original source The frost heaving forces developed under a 1 ft. (30.5 cm) diameter steel plate were measured in the field throughout one winter. The steel plate was fixed at the ground surface with a rock-anchored reaction frame.
Heave gauges and thermocouples were installed at various depths to determine the position and temperature of the active heaving zone. The general trend was for the surface force to increase as the winter progressed. When the frost line approached the maximum depth the force was in excess of 30,000 lb (13,608 KG). Estimates of the heaving pressure at the frost line ranged from 7 to 12 psi (0.49 to 0.84 KG/cm) square during this period. The variation of surface heaving force was closely associated with weather conditions. Warming trends resulting in a temperature increase of the frozen layer caused the forces to decline. 1 Sarah Cervone, web page data from the APIRS database, Graphics by Ann Murray, Sara Reinhart and Vic Ramey, Vic Ramey is the editor.
DEP review by Jeff Schardt and Judy Ludlow. 120 Carlton Street Suite 407, Toronto ON M5A 4K2. Tel: (416) 964-9415 1-800-268-7070 Email:. The firm provides professional & &.
Alan Carson is a past president of ASHI, the American Society of Home Inspectors. Thanks to Alan Carson and Bob Dunlop, for permission for InspectAPedia to use text excerpts from The Home Reference Book & illustrations from The Illustrated Home. Carson Dunlop Associates' provides extensive home inspection education and report writing material. illustrates construction details and building components, a reference for owners & inspectors.
Special Offer: For a 5% discount on any number of copies of the Illustrated Home purchased as a single order Enter INSPECTAILL in the order payment page 'Promo/Redemption' space. to manufacturer's model and serial number information for heating and cooling equipment, useful for determining the age of heating boilers, furnaces, water heaters is provided by Toronto - Carson Dunlop Weldon & Associates Special Offer: Carson Dunlop Associates offers InspectAPedia readers in the U.S.A.
A 5% discount on any number of copies of the Technical Reference Guide purchased as a single order. Just enter INSPECTATRG in the order payment page 'Promo/Redemption' space., Carson Dunlop & Associates, Toronto, Ontario, 25th Ed., 2012, is a bound volume of more than 450 illustrated pages that assist home inspectors and home owners in the inspection and detection of problems on buildings. The text is intended as a reference guide to help building owners operate and maintain their home effectively. Field inspection worksheets are included at the back of the volume. Special Offer: For a 10% discount on any number of copies of the Home Reference Book purchased as a single order. Enter INSPECTAHRB in the order payment page 'Promo/Redemption' space. InspectAPedia.com editor Daniel Friedman is a contributing author.
Or choose the for PCs, Macs, Kindle, iPad, iPhone, or Android Smart Phones. Special Offer: For a 5% discount on any number of copies of the Home Reference eBook purchased as a single order. Enter INSPECTAEHRB in the order payment page 'Promo/Redemption' space. Building inspection education & report writing systems from.
protocol ASTM Standard E 2018-08 for Property Condition Assessments. including home study & live classes at eleven colleges & universities. ASHI@Home Training 10-course program.
Special Offer: Carson Dunlop Associates offers InspectAPedia readers in the U.S.A. A 5% discount on these courses: Enter INSPECTAHITP in the order payment page 'Promo/Redemption' space. InspectAPedia.com editor Daniel Friedman is a contributing author. manages business operations,scheduling, & inspection report writing using Carson Dunlop's knowledge base & color images. The Horizon system runs on always-available cloud-based software for office computers, laptops, tablets, iPad, Android, & other smartphones.